Application of Ferric Chloride Etching Technology in PCB Manufacturing
This article was last updated on August 14, 2024
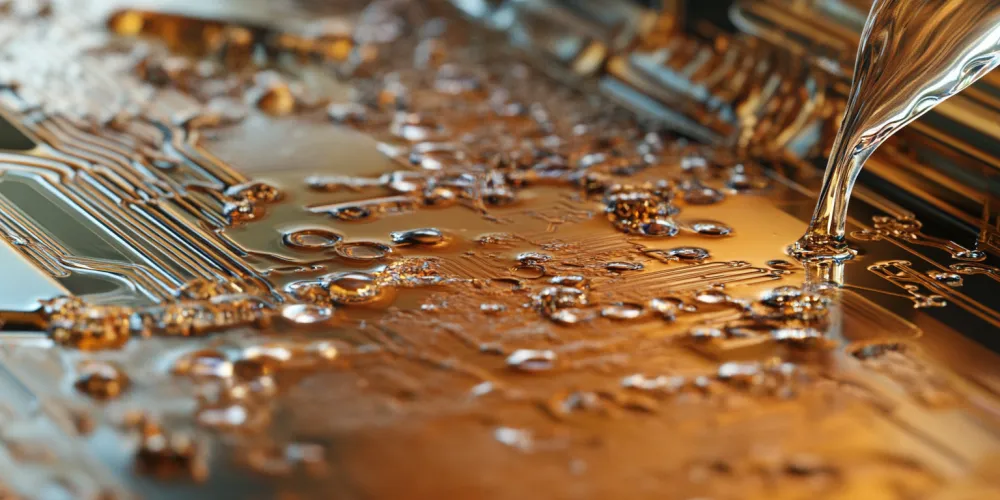
Applications and Advantages of Ferric Chloride Etching Technology
In the manufacturing of Printed Circuit Boards (PCBs), Ferric Chloride (FeCl₃, Iron(III) Chloride) etching technology is a widely applied and mature process. This technique uses a ferric chloride solution to selectively etch copper foil, creating the desired circuit patterns. In this process, ferric chloride plays a crucial role, effectively converting copper (Cu) into soluble copper chloride (CuCl₂).
This technology is widely recognized in the industry for its following advantages:
- High Efficiency: Ferric chloride etching speed is relatively fast, significantly improving production efficiency.
- Cost-Effective: Ferric chloride is relatively inexpensive and can be reused multiple times, reducing production costs.
- Wide Applicability: Suitable for etching copper foils of various thicknesses with high process stability.
- Easy Operation: The process is mature and easy to control, making it suitable for large-scale applications.
- Environmentally Friendly: Compared to acidic etchants, ferric chloride has a smaller environmental impact, making waste liquid treatment easier.
Ferric Chloride Etching Process
The process of Ferric Chloride etching technology is already quite mature, usually consisting of the following steps:
- Pre-treatment: Clean the PCB surface, removing grease and oxides to prepare for subsequent etching.
- Resist Coating: Apply a protective layer to areas that do not require etching to prevent ferric chloride from corroding these areas.
- Etching: Immerse the PCB into the ferric chloride solution to etch, forming precise circuit patterns.
- Rinsing: Rinse the PCB with water to remove residual ferric chloride solution.
- Drying: Dry the PCB using hot air or an oven, preparing it for subsequent processes.
- Inspection: Conduct quality checks to ensure the etching meets standards.
Continuous Improvement and Technological Innovation
Although Ferric Chloride (FeCl₃, Iron(III) Chloride) etching technology is already mature, the industry is continually exploring improvements and innovations. Recent developments include the application of intelligent solution management systems that monitor the concentration and pH of the solution in real-time, ensuring stability and consistency in the etching process.
Additionally, significant progress has been made in the development of waste liquid treatment and resource recovery systems. These systems can effectively convert the waste liquid from the ferric chloride etching process into reusable resources, further reducing the environmental impact and enhancing the environmental friendliness of the product.
Future Prospects
With the continuous innovation of electronic products and the growing demand from the market, Ferric Chloride (FeCl₃, Iron(III) Chloride) etching technology will play an even greater role in a wider range of applications. Future research and development may focus on:
- Improving etching accuracy to accommodate higher-density PCB designs.
- Further optimizing process parameters to increase production efficiency.
- Developing more environmentally friendly ferric chloride formulas and recycling technologies.
Ferric Chloride etching technology plays a key role in PCB manufacturing. Through continuous technological innovation and process optimization, this technology will continue to provide efficient and environmentally friendly solutions for the electronics manufacturing industry.