Breakthrough in Copper Powder Quality Control Technology
This article was last updated on August 12, 2024
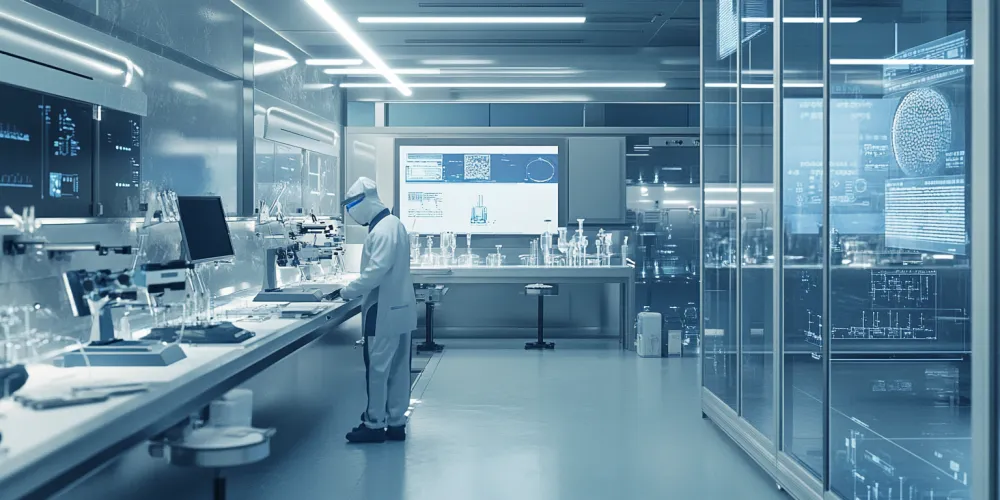
Background and Significance of Technological Innovation
Striving for excellence, quality first.
In the context of the rapidly developing technology industry, Copper Powder has become a critical raw material in electronics manufacturing, and its quality control has become a key focus for the industry. As consumer electronics continue to evolve toward lighter and smaller designs, the quality requirements for metallurgical Copper Powder have also become more stringent. Particularly in the application of submicron particle size technology and conductive paste, material stability is crucial. Under this trend, technological innovation has become the only way to enhance product competitiveness.
Metallurgical Copper Powder plays a pivotal role in the manufacturing process of electronic products, and its quality directly affects the performance and reliability of the final product. Although traditional quality control methods have been used for many years, they have become inadequate in the face of increasingly stringent product specifications. Therefore, the industry is constantly seeking breakthroughs, developing more precise and efficient quality control technologies.
Against this backdrop, several new technological directions are gradually emerging:
- Application of intelligent monitoring systems
- Utilization of big data analysis in quality control
- Development of precise control technology for submicron particle sizes
- Research on eco-friendly production processes, particularly the development of porous materials and metal matrix composites
These new technologies not only have the potential to improve the quality stability of metallurgical Copper Powder but may also bring revolutionary changes to the entire industry. In the precision manufacturing industry, companies have already begun to develop and apply these related technologies.
The industry is well aware that continuous innovation is the only way to stay competitive in the highly competitive international market. Therefore, many companies are actively investing in research and development resources, committed to developing the next generation of metallurgical Copper Powder quality control technology, contributing to the precision manufacturing industry.
Core Content of the New Technology
Details determine success, innovation changes the future.
The core of the new generation of metallurgical Copper Powder quality control technology lies in intelligent monitoring and real-time adjustment throughout the entire process. This technological breakthrough is mainly reflected in the following aspects:
- Intelligent sensor network:
- Deploy high-precision sensors at critical points in the production line
- Monitor key parameters such as temperature, humidity, and pressure in real-time
- Establish a comprehensive data collection system
- AI-driven quality prediction models:
- Use machine learning algorithms to analyze massive production data
- Build accurate quality prediction models
- Provide early warnings of potential quality issues
- Automated control system:
- Automatically adjust production parameters based on AI model predictions
- Ensure product quality stability
- Submicron particle size control:
- Develop high-precision particle size analysis technology for submicron particle size control
- Achieve precise control of copper powder particle size
- Improve product uniformity and stability, especially in MLCC, conductive paste, EMI shielding, and absorbing materials applications
The application of this new technology enables precise control, real-time monitoring, and intelligent adjustment in the production process of metallurgical Copper Powder. For example, when an intelligent sensor detects a slight deviation in temperature at a certain production stage, the AI system immediately analyzes the potential impact of this deviation on the final product quality. If the prediction indicates that it may lead to uneven particle size, the system will automatically fine-tune the heating power or cooling speed to ensure that the entire batch meets the expected quality standards.